The Hidden Costs of Smelting Electronics
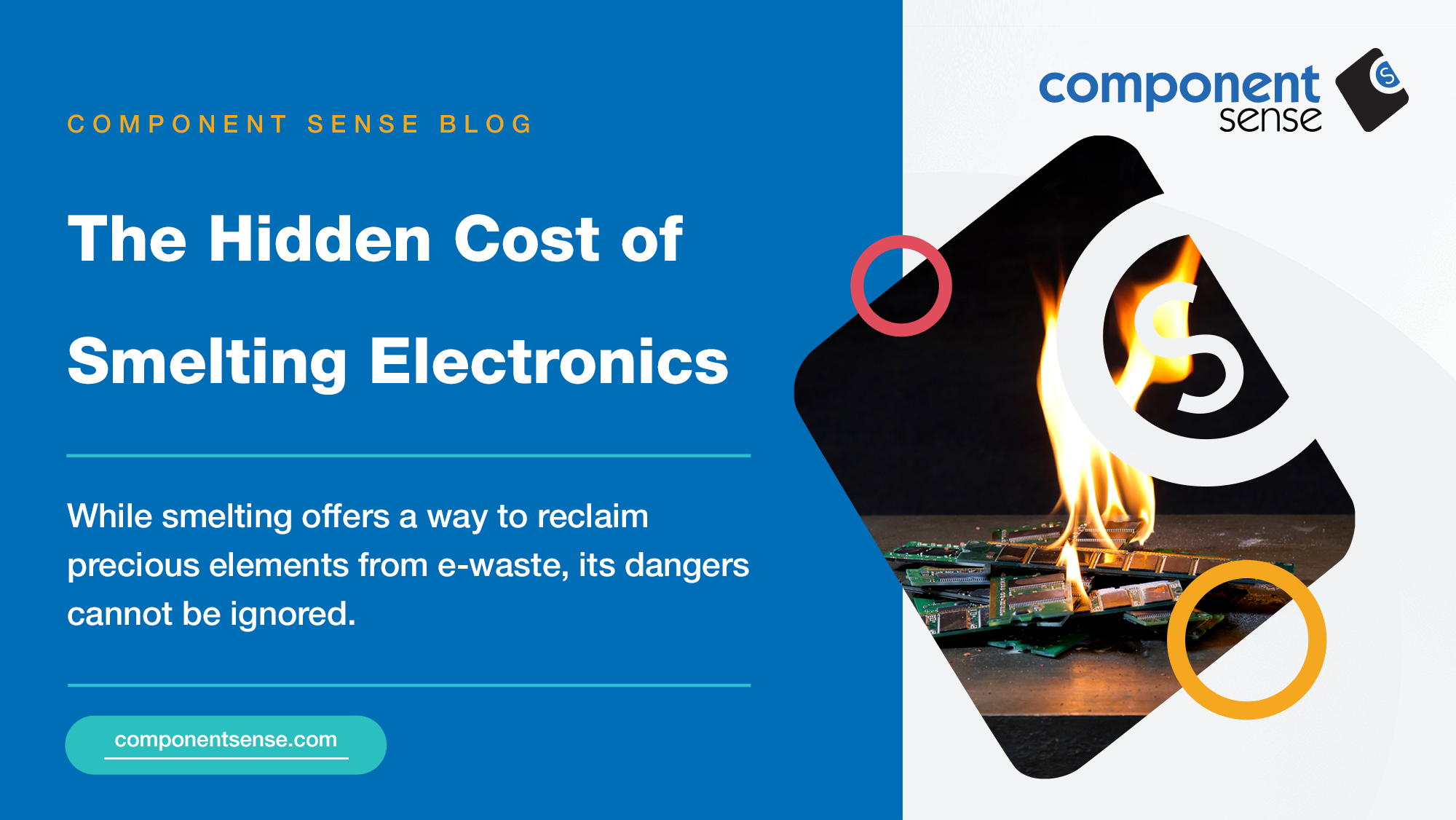
Electronic waste, or e-waste, poses a growing challenge globally.
One method stands out as we seek ways to minimise pollution and reclaim valuable rare earth elements: smelting. This popular but controversial practice has far-reaching implications for both our environment and health.
The environmental and health implications of smelting are often overlooked, casting a shadow on its sustainability. This article will peel back the curtain to reveal the full picture of this heated recycling topic.
The process of smelting electronics
The scarcity of rare earth elements (REEs) is one of the key drivers for smelting as a popular recycling solution. This method heats e-waste to the desired temperature to extract valuable minerals and melt away what is not needed. Smelting varies in technique but often involves either acids or bonfires. While some commercial ventures smelt e-waste at scale, unregulated and particularly dangerous operations are also prevalent in lesser-developed nations.
Issues with smelting
In some cases, plastic in e-waste may take up to 1 million years to decompose. Meanwhile, aluminium can take between 50 and 500 years to break down. It may seem like melting e-waste is the perfect option to keep electronics out of landfills and recycle rare earth metals back into a circular economy, but some things in life are indeed too good to be true.
Environmental damage
The Basel Convention labels e-waste as hazardous due to toxic substances like mercury and lead. When smelted, these chemicals do not simply vanish. Instead, they contaminate the air and local environment, harming nearby habitats,living organisms, and even human health.
Health risks
As these harmful contaminants emanate from open burning to the surrounding soil, water sources, and atmosphere, workers also inhale fumes and particulate matter. This intake puts people at risk of respiratory issues and other diseases. A stark example of the mishandling of e-waste is Agbogbloshie in Ghana, where financial necessity drives dangerous recycling practices by hand.
Energy use
The energy demand for smelting e-waste is exceptionally high, with temperatures needed to exceed 800 degrees Celsius in some cases. This process, often reliant on substantial electricity or fossil fuels, also contributes to greenhouse gas emissions. If smelting was powered by reusable energy, it may paint a more sustainable picture.
“Recycling any material, even cardboard, requires energy. Recycling electronics requires an awful lot of it,” explained Component Sense Marketing Manager, Morag Dine.
Reducing the need for smelting
At Component Sense, we agree that smelting is the lesser of two evils when compared to dumping e-waste in landfills. However, our business is driven to lead electronic manufacturers to tackle e-waste at the source. Reducing consumption and promoting a circular economy is far more sustainable than recycling.
Better forecasting
Overproduction and over-forecasting are major contributors to the world’s e-waste problem. By better aligning production with actual demand, we can significantly reduce surplus inventory and its conversion into e-waste.
With recent advancements in artificial intelligence (AI), it is now easier than ever for procurement experts to predict precisely what is required for their supply chain. AI predictive analytics are helping electronic manufacturers to analyse market conditions, understand consumer behaviour, and track product life cycles more accurately.
“Ultimately, everything we create comes from a resource. Even manmade resources come from natural sources in some way,” said Morag.
Ethical procurement
Electronic manufacturers carry a significant responsibility for their supply chains, extending to ethical and sustainable procurement. At Component Sense, we advocate for using excess components rather than direct purchases when possible. This not only prevents potential smelting but also promotes circularity in material use.
The goal of circularity is to keep materials and products in circulation at their highest value for as long as possible. As well as sourcing components from trusted grey market suppliers, it is vital for companies not to fall into the trap of planned obsolescence. Adopting modular designs that allow for easier upgrades and repairs can extend product lifespans.
Redistribute before recycling
- Reduce
- Reuse
- Recycle
An essential observation of this famous sustainability ethos is the order in which this guidance appears. Redistributing (or reusing) comes before recycling in the famous three Rs for a reason. Electronic manufacturers should redistribute their excess and obsolete (E&O) component stock to reduce the need for smelting. That way, another company can put brand new parts to good use that would otherwise end up as e-waste.
Reselling excess stock makes financial sense as well. Holding on to too much stock can negatively impact your bottom line in more ways than one. By choosing a redistribution model like Component Sense’s InPlant™, you can often get 100% of the cost of your excess components.
“Think about what you originally invested in a component. When you redistribute with Component Sense, you get a large portion of your money back. The economy of scale means we pass on savings to buyers whilst maximising your returns,” explains Morag.
Want to learn more about excess redistribution?
While smelting offers a way to reclaim precious elements from e-waste, its hidden costs — from environmental damage to health risks — cannot be ignored. Innovative approaches and responsible practices are essential for a sustainable future. Take a proactive step to prevent the need for smelting by emailing us today: