Top Tips to Maximise Your Electronic Component Warehouse Space
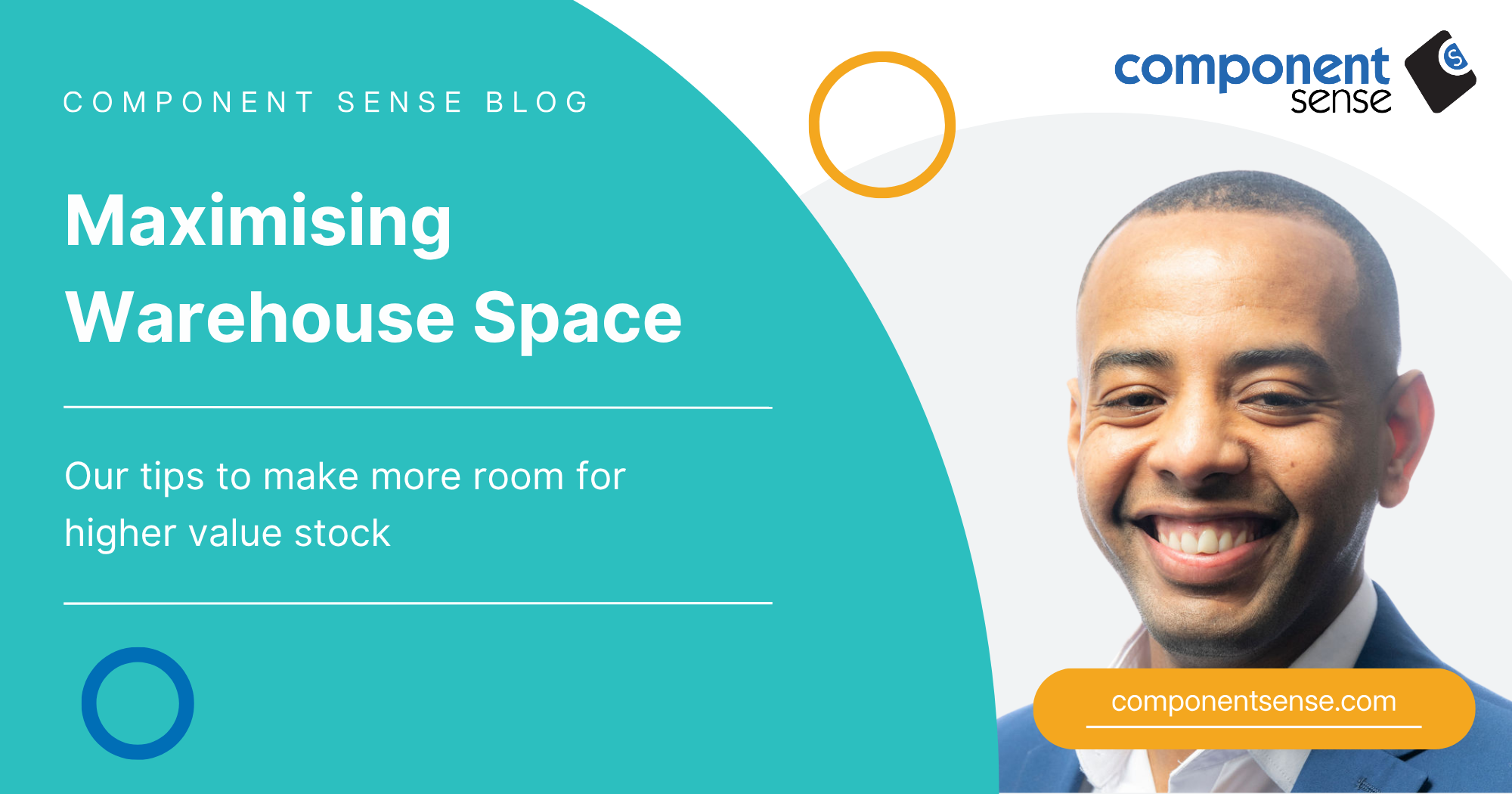
A warehouse might appear as a large, expansive area to the untrained eye. Yet, Warehouse Managers know appearances can be deceptive.
At Component Sense, our experience spans EMSs (electronics manufacturing services) and OEMs (Original Equipment Manufacturers) of all sizes. The logistics personnel we talk to all share a common challenge: warehouse space.
We spoke with Component Sense Operations Manager, Ben Dent, to find out what advice he would give to electronic manufacturers wanting to make the best possible use of their warehouse space. Maximising your warehouse space does not just relate to square footage but also labour and component margins.
1. Automate where possible
Automation employs technology to minimise human input, significantly reducing manual handling in warehouses. The global automation market is expected to grow by over $26bn by 2026, proving its popularity.
Investing in automation is the key to unlocking valuable time and money. An example of automation in action is utilising an AS/RS (automated storage and retrieval system) to increase storage density and more accurately manage your inventory. While this may instil images of robot arms picking up boxes, simple SAP integrations or conveyor belts can be equally effective.
The use of AI in warehouses is also exciting and may remove human error from many processes, including better forecasting. Not to mention, AI can free up time for warehouse teams to focus on more important issues.
“Automation does not need to be on a SAP management system, although this is the most commonly used warehouse system. For companies wanting to automate the management of their excess, Component Sense’s InPlant™ system is a great example of automation,” said Ben.
2. Have regular cycle counts
Regular cycle counts are essential for accurate shelf inventory, allowing early identification of discrepancies or excess. Many larger companies already build regular cycle checks into their processes to stay compliant. However, we do still see some EMSs not prioritising accurate inventory data.
At Component Sense, we recommend daily checks for excess and obsolete (E&O) stock. Regularly identifying and removing surplus inventory frees up space for higher-priority parts. In many cases, warehouse staff can pull a velocity report from their WMS (warehouse management system) to check the pick frequency of each SKU (stock-keeping unit) and identify components for removal.
“E&O stock needs to be monitored straight away. Do not leave it in the corner, gathering dust. Otherwise, you will miss the boat. Automated daily checks can help here,” explained Ben.
3. Label everything
Accurate inventory data is crucial for utilising all storage space efficiently, making labels essential. They ensure seamless tracking of stock levels and movements for every component.
Implementing RFID (radio frequency identification) labels means you can simply walk down aisles in your warehouse and scan what you need. As well as improved inventory accuracy and operational efficiency, labels also help with redistributing your excess. Lack of data and missing labels are some of the common inventory mistakes we see at Component Sense.
Assigning a unique GRN number to each shipment is crucial, especially when the same component arrives multiple times. Without this, tracking and managing stock becomes challenging.
“Some of our suppliers have introduced a one-scan system for their stock. When stock comes in, a single scan is all that is needed for all key information to be added to their SAP. Component Sense then receives an automated report every day to help us actively manage their excess inventory,” said Ben.
4. Prioritise component stock by date code
Optimise warehouse space by categorising high-priority components, similar to rotating drinks in a fridge. At Component Sense, we advise against FIFO (first in, first out) methods, which often result in wasted space and obsolete stock.
The FEFO (first-expired, first-out) method quickly identifies excess stock for redistribution, maximising returns while the items are still valuable. At Component Sense, we also recommend separating incoming and outgoing goods to streamline warehouse operations and reduce confusion.
“Many of our buyers ask for a specific part but ignore date codes. This means they keep getting in new parts, and the old ones remain unused until they are obsolete,” explained Ben.
5. Store excess off-site
Excess stock not only affects finances but also consumes valuable warehouse space. With many manufacturers holding E&O inventory worth 10% of their revenue, the impact on warehouse capacity can be significant.
Some companies are put off from redistribution as they do not want to pay for storage while parts are listed. Thanks to Component Sense’s partnership with logistics company DSV, we can consign your excess while it is stored at a local DSV warehouse. This storage and insurance is free of charge to you.
Want to make warehouse space by redistributing excess stock?
Embracing these tips will unlock warehouse space, ensuring you have room for higher-margin stock and remain agile. Solutions like Component Sense InPlant™ or Consignment effectively manage surplus stock, turning it into effortless revenue.
To maximise your warehouse space, speak to one of our experts about redistributing your excess and obsolete inventory. Email us today.