10 Ways to Improve Warehouse Efficiency
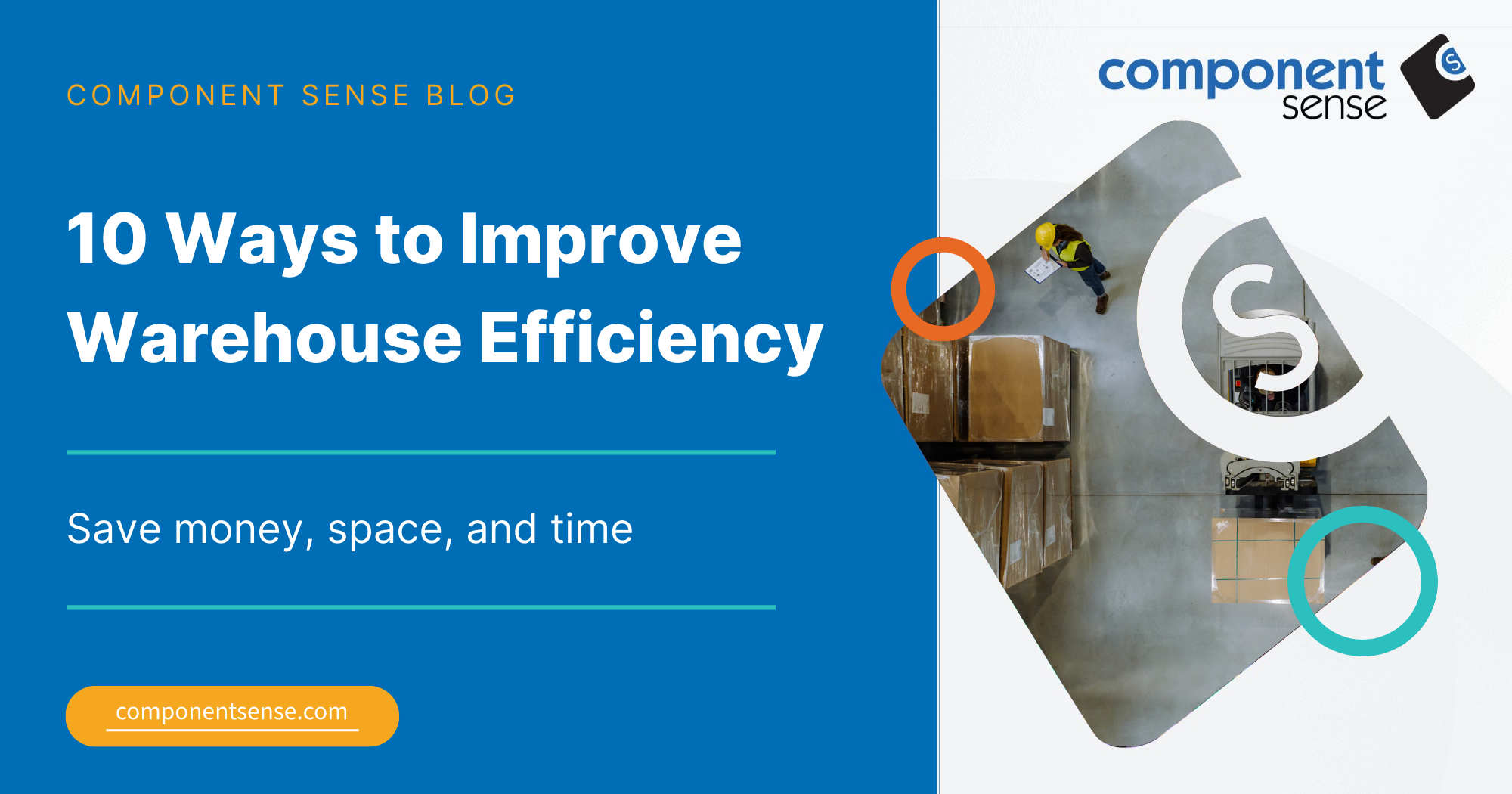
As the last five years have taught us, the electronics sector can be unpredictable.
Severe weather events, a global pandemic, geopolitical uncertainties, and tariffs all cause headaches for supply chain and logistics professionals.
Now more than ever, optimising your warehouses and operations within them is critical to remain agile and responsive to often uncontrollable external factors. An efficient warehouse can also be a competitive edge in the highly competitive electronic manufacturing market.
Efficient operations enable quicker order fulfilment, free up space, and reduce costs. Here are 10 general considerations for areas you may be able to improve.
1. Redesign your warehouse layout
Your warehouse space is like a blank canvas, waiting to be filled with ideas to utilise the area best. Taking a step back and conducting a space utilisation audit is a practical first step to identify underused regions and the movement patterns of staff to see congestion points and sub optimal routes.
Once you have a clear idea of where you are lacking, you can implement new, shorter pathways for goods. Placing high-volume stock near packing areas is an example of this to make picking faster. Consider vertical racking and mezzanines if there is only room for incremental gains.
Top tip: The ABC method for inventory can be helpful in this process.
2. Redistribute excess and obsolete stock
Each shelf in your warehouse should be seen as a financial opportunity. You want to ensure that your space holds the highest-value components possible. Slow-moving, excess-to-requirements, or obsolete parts mean space is unnecessarily being taken up that could instead hold higher-value stock.
Regularly reviewing and redistributing excess and obsolete (E&O) components frees up space, recoups some or all of the financial value of the unwanted inventory, and avoids costly write-offs or paying for disposal. E&O can greatly impact your finances, so working with a trusted component redistributor like Component Sense can improve your bottom line.
3. Improve stock visibility
Smart technology also presents an opportunity for greater stock visibility. To make improvements to warehouse management, precise data and knowing what is on your shelves are crucial.
While you probably also have a WMS (warehouse management system), no two systems are created equal. While barcode systems are widely used, utilising RFID (radio frequency identification tags) means you can locate and track component stock with less manual intervention.
4. Create a culture of feedback and innovation
Your warehouse staff are the ones experiencing and living your warehousing principles every day. Empowering them to speak up and make suggestions to improve their daily experience will often lead to broader operational improvements.
By involving warehouse team members in the improvement process, you can create a sense of ownership among staff, which will help make efficiency improvements stick. Another useful idea is to create trial periods for testing new ideas. That way, only successful ideas will be scaled and implemented in the long run, and there is less risk for counterproductive changes.
5. Implement lean warehousing principles
A lean approach to inventory management can lead to efficiencies in your warehouse. In the same way that it can be useful to evaluate your warehouse design and layout, systems and processes should also be reviewed regularly. That way, you can look to reduce any bottlenecks and unnecessary handling.
Top tip: The 5S method can be a productive place to start when applying lean warehousing principles.
6. Adopt automation where appropriate
With advancements in AI and automation, there are nearly countless opportunities to use these technologies to drive warehouse efficiencies. While AI has the potential to support more accurate forecasting and prevent overstocking, it is still early days.
Over the recent decade, many warehouses have implemented AGVs and conveyor belts to move materials, especially on a large scale. Robotic picking systems are gaining popularity, and technologies like this are only becoming more accessible to companies of all sizes.
Calculating the ROI (return on investment) on potential automation technology by weighing reduced labour costs against increased throughput can be a helpful place to start.
7. Train and empower your workforce
Having the right people in the correct positions is crucial to an efficient warehouse. While incorporating new technologies is important, ultimately, these tools will not be nearly as impactful without the right people operating them.
A comprehensive onboarding and training approach is key to getting new hires up to speed and effective as soon as possible. Having a tried, tested, and consistent onboarding system in place and easy-to-follow SOPs (standard operating procedures) reduces room for errors and gets all team members on the same high-performing page.
8. Forecast demand to prevent overstock
While redistributing E&O stock is a valuable tool to prevent overstock taking up room in your warehouse, a proactive approach to minimising the potential for E&O in the first place is also needed.
In turbulent times, it may seem tempting to take a conservative approach to forecasting components. However, this often leads to underutilised shelving, missed opportunities, and the creation of e-waste. In the bigger picture, we believe a ‘less is more’ approach to forecasting is not only better for your bottom line but also for the environment.
There are many ways to ensure more accurate component forecasting, including investing in cutting-edge forecasting tools that provide alerts for reordering. Your own historical data may also help you determine how much buffer you realistically need.
9. Encourage cross-functional collaboration
Teamwork makes the dream work. When the broader company works together for a common goal, it drives efficiencies across the board.
Enabling regular communication between procurement, finance, and warehouse teams creates a clear understanding. It means updates can be shared regarding stock levels, incoming orders, and, of course, the needs of partners or customers.
10. Use data and metrics for continuous improvement
Data and analytics are key when taking stock of what is and is not working in the warehouse. Only by painting a truthful picture of what is and is not working can you make meaningful improvements to efficiency.
Always pay close attention to information in your WMS regarding picking accuracy, cycle times, and physical count accuracy. Creating a comprehensive but easy-to-understand dashboard can also help multiple stakeholders within the company quickly visualise what is going on.
Once data and reporting are in place, you can create a roadmap for testing ideas and setting goals for improvements related to key metrics. You can also establish benchmarks against historical data or industry best standards.
Free up warehouse space with Component Sense
Component Sense is a trusted redistributor of excess and obsolete component inventory. We help large OEMs (original equipment manufacturers) and EMSs (electronic manufacturing services) recoup the financial value of their surplus inventory and reduce e-waste. By redistributing unwanted components, your warehouse becomes more efficient, and there is more shelf space for higher-value parts and responding to market conditions.